Prefabricated buildings, or prefabs, are transforming the manufacturing and construction industries with their efficiency, sustainability and flexibility. Technology plays a pivotal role in enabling this transformation, making prefabrication not only viable but also highly efficient, scalable and sustainable.
Let’s explore how technology helps streamline and improve the process of designing, manufacturing and assembling prefabs.
Read: 5 Top IT Trends Transforming Construction and Design
Building Information Modeling (BIM)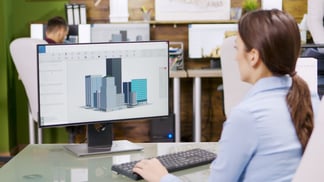
BIM technology allows architects, engineers and construction professionals to create detailed, immersive digital models of buildings before any physical construction begins, ensuring a high level of efficiency. These 3D models provide a comprehensive visualization of the project, highlighting structural components, electrical systems, plumbing and more.
BIM also fosters seamless collaboration by allowing different teams to access and edit the same model in real-time. This minimizes misunderstandings and miscommunication between teams, leading to fewer mistakes and changes down the line. It also allows the teams to identify potential issues early on, reducing costly errors and delays.
Automation and Robotics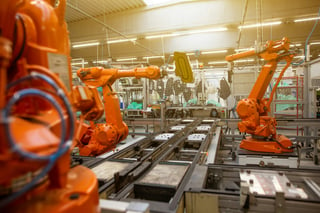
Robotics in factory settings allow for the automated production of building components with extreme precision and efficiency. Automated systems can cut materials, assemble components and even conduct quality control checks, all while reducing human error and labor costs.
Robotics and automation drastically reduce the time required to create building components, accelerating the entire construction process and helping meet deadlines more consistently.
Internet of Things (IoT) and Smart Devices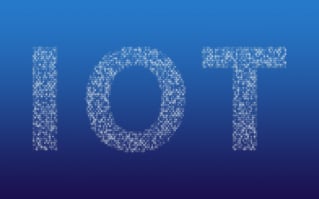
IoT sensors can be embedded within prefabricated components to monitor their conditions, such as humidity, temperature and structural stability. This real-time data helps ensure that components maintain quality and adhere to safety standards. After installation, IoT-enabled prefabs can continue to be monitored for wear and tear, allowing for preventative maintenance and extending the building’s lifespan.
IoT can also track the movement of materials and components from the factory to the construction site. This ensures timely delivery and reduces downtime, optimizing the supply chain and reducing delays.
Artificial Intelligence (AI) and Data Analytics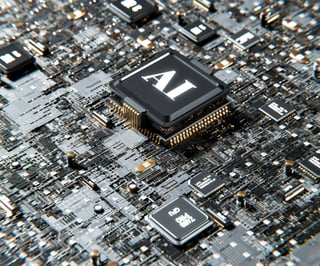
AI-driven algorithms analyze past projects, environmental factors and client requirements to suggest optimized designs. AI can quickly assess factors such as energy efficiency, material costs and structural integrity, allowing for more intelligent design decisions. It can also identify defects and inconsistencies in building components, ensuring high-quality standards.
Predictive analytics help construction firms forecast costs, timelines and potential risks by analyzing historical data to predict potential challenges and optimize schedules. This information is valuable for project planning, enabling companies to anticipate challenges and allocate resources more effectively.
Read: AI for Your Industry: Construction and Design
Cloud Computing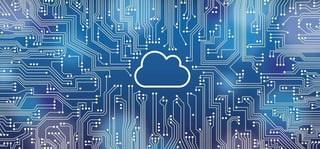
Cloud-based platforms allow teams to assess project data from anywhere, enabling remote collaboration across various locations. This is especially useful for prefab projects, where manufacturing and construction might happen in different places.
Cloud computing also enables centralized data management, which means that all project files, documents and designs are stored securely and can be accessed by authorized personnel at any time, improving workflow and decision-making.
Drones, Augmented Reality (AR) and Virtual Reality (VR)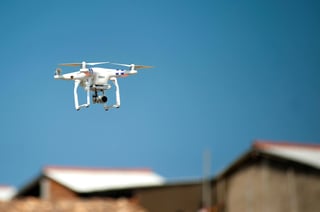
Drones provide a quick and accurate way to survey construction sites and monitor project progress. They can capture aerial views and high-resolution images, helping teams assess site conditions and plan accordingly. Drones can also enable remote inspections, allowing supervisors and stakeholders to review project progress without physically being on-site. This saves time and can speed up the approval process for various stages of the construction project.
AR and VR can provide numerous benefits. AR can be used on-site to overlay digital information and visualize where prefabricated components should be placed on the physical construction site. Using AR headsets or mobile devices allows construction workers to see exactly where each part fits, reducing assembly errors and improving installation efficiency. It can also guide workers through assembly processes and highlight potential hazards. VR allows stakeholders to take virtual tours of prefabs, providing a realistic sense of scale and layout.
Sustainable and Energy-Efficient Designs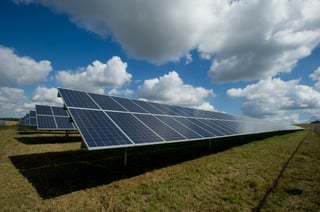
Many prefab projects incorporate renewable energy sources, such as solar panels, smart thermostats and efficient HVAC systems, thanks to advancements in sustainable technology. Software tools can simulate energy consumption and suggest energy-efficient solutions, reducing the building’s overall carbon footprint.
Technology also aids in selecting sustainable materials, like recycled steel or low-carbon concrete, which are easier to produce and more durable. This helps ensure that prefabs meet green building standards and contribute to environmental conservation.
Blockchain for Transparent Contracts and Supply Chains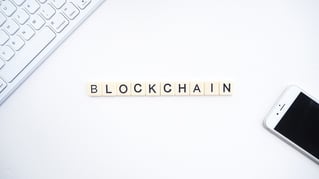
Blockchain technology can track materials throughout the supply chain, providing transparency and preventing fraud. All parties involved in the construction process can verify the origin, quality and movement of materials, enhancing trust and accountability.
Blockchain enables the use of smart contracts, which are self-executing contracts with terms written into the code. These can automatically release payments when certain conditions are met, such as the delivery of components, which reduces administrative overhead and speeds up transactions.
Read: Robots, Drones, AI – Oh, My! Innovative Technologies for Construction
Enhance Your Firm with Thriveon
As technology continues to advance, the prefab industry will likely see even more improvements, enabling faster project timelines, reduced costs and greener building practices. To stay ahead of the competition and be aware of the latest developments, consider partnering with Thriveon.
Schedule a meeting now for more information.