Workforce development is essential to sustain growth in industries like construction and manufacturing, where technological advancements and increasing complexity create both opportunities and challenges. As industries continue to evolve and face ongoing challenges with workforce shortages, employee skill gaps and shifting demands, technology plays a pivotal role in shaping the workforce, enhancing skill development and driving overall productivity.
By providing a workforce development solution, technology equips employees with the right skills, improves efficiency and drives growth, ensuring long-term success in today’s competitive landscape.
Read: Robots, Drones, AI – Oh, My! Innovative Technologies for Construction
1. Bridging the Skills Gap Through Training and Upskilling Programs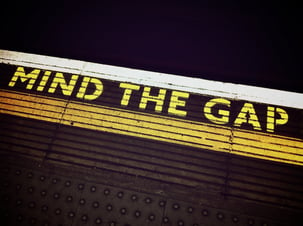
One of the most significant ways technology aids workforce development is through digital training and upskilling platforms. For industries like construction and manufacturing, where precision and technical skills are crucial, these platforms allow employees to learn advanced technologies at their own pace, often through virtual reality (VR) or augmented reality (AR) simulations.
Workers can practice complex tasks in an immersive, risk-free environment, making it easier to learn concepts, develop practical skills and gain real-world experience before stepping onto a job site. For example, construction workers can use VR to practice operating heavy machinery and learn how to avoid errors and accidents.
2. Enhancing Collaboration and Communication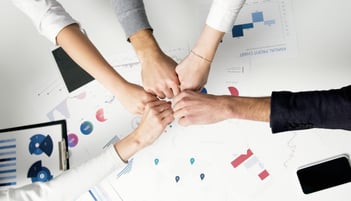
Remote learning and effective communication and collaboration have become increasingly important in today’s modern workplace. Technologies like cloud-based platforms, team collaboration software and mobile applications enable workers to communicate remotely in real-time. For example, building information modeling (BIM) in construction revolutionizes collaboration by allowing stakeholders to work on a single digital model of a project.
For companies that need to provide ongoing education to their workforce, collaboration tools like Microsoft Teams and Zoom enable workers to participate in training sessions, access resources and collaborate on projects from any location. This helps ensure that employees in geographical locations receive consistent training and development opportunities. For example, manufacturers can host virtual training workshops on new equipment, ensuring all workers receive real-time updates on how to operate it.
3. Increasing Productivity with Automation and AI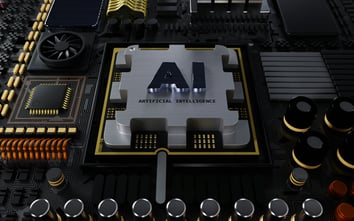
Automation and artificial intelligence (AI) have transformed workforce management by handling repetitive tasks and streamlining workflows, allowing employees to focus on higher-value activities. AI can handle workforce scheduling by analyzing production data to assign the right workers to the right tasks based on skills and availability, leading to improved productivity. Robotics and the Internet of Things (IoT) devices are also reshaping work processes by reducing human error and increasing precision.
In manufacturing, AI can predict maintenance needs for machinery, schedule work shifts and optimize production timelines, leading to a more efficient workforce and less downtime. Meanwhile in construction, 3D printing is speeding up the building process.
Read: A Guide to Industry 4.0: The Future of Manufacturing
4. Enhancing Safety Through Technology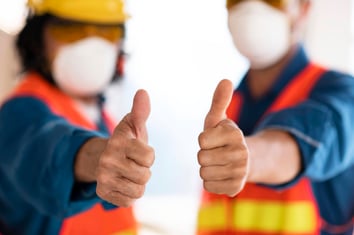
In industries like construction and manufacturing, safety is a top concern; workers are often exposed to hazardous environments. Technology plays a pivotal role in protecting workers through innovations like wearable devices, drones and IoT-enabled sensors that monitor environmental conditions. These tools can alert workers and supervisors to potential risks, enabling them to take proactive measures to ensure safety on the job site. By integrating these technologies into workforce development, companies can ensure their workers are better prepared for and protected against potential hazards.
5. Making Data-Driven Decisions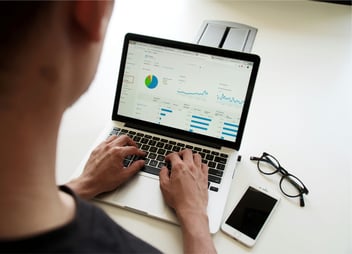
The integration of Big Data and analytics into workforce development allows businesses to make more informed decisions about training needs, workforce planning and productivity improvements. Construction and manufacturing companies can collect and analyze data on employee performance, training outcomes and operational efficiency, helping them identify gaps, take actionable steps to enhance workforce development and ensure that workforce development initiatives align with evolving demands and needs. For example, analytics can reveal a particular manufacturing process that consistently causes bottlenecks, prompting leadership to provide additional training or invest in more efficient equipment.
6. Recruiting and Talent Acquisition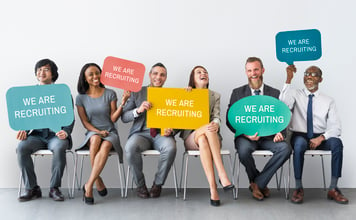
Technology not only aids in developing current workers but also plays a crucial role in attracting and hiring new talent. AI-driven recruitment tools help organizations find candidates with the right skills and qualifications, speeding up the hiring process. AI algorithms can screen resumes and identify top candidates for skilled positions, saving HR departments time and ensuring the best talent is brought on board.
Read: 5 Top IT Trends Transforming Construction and Design
Challenges and Opportunities
While technology offers significant benefits, it can also present challenges. Issues like digital literacy, privacy concerns and the potential for job displacement must be addressed. However, by investing in technology and training, you can create a workforce that is better equipped to meet the demands of the future.
Partner with Thriveon
As technology continues to evolve in the manufacturing and construction industries, these industries must adapt and embrace these innovations to ensure a thriving and competitive workforce. However, if you don’t know where to start with this transformation, don’t fret – partnering with a managed service provider like Thriveon is the answer.
Our managed IT and modern office IT services ensure that your business utilizes cutting-edge technology to maximize your investment. We also align your company to over 500 industry best practices to ensure your organization is competitive and relevant.
Schedule a meeting today for more information.